Hydrogen Steam Boiler Calculator
Size a hydrogen steam boiler
Steam Boiler Calculator Equations
Annual Steam Required
\[ Q_{steam} = D \times N_{days} \times H_{daily} \]
Where:
- \( D \) = Steam rate (ton/h)
- \( N_{days} \) = Annual operating days
- \( H_{daily} \) = Daily operating hours
Heat Required
\[ Q_{heat} = \frac{Q_{steam} \times 1000 \times (h_{steam} - h_{feed})}{3.6 \times 10^6} \]
Where:
- \( h_{steam} \) = Steam enthalpy (kJ/kg)
- \( h_{feed} \) = Feedwater enthalpy (kJ/kg)
- \( T_{feed} \) = Feedwater temperature (°C)
Annual Fuel Required
\[ Q_{fuel} = \frac{Q_{heat}}{\eta_{burner}} \]
Where:
- \( \eta_{burner} \) = Burner efficiency
Hydrogen Demand
\[ m_{H_2} = \frac{Q_{fuel}}{N_{days}} \times \frac{1000}{33.33} \times \frac{E_{H_2} \times f_{blend}}{E_{fuel} \times (1 - f_{blend}) + E_{H_2} \times f_{blend}} \]
Where:
- \( E_{fuel} \) = Fuel energy density (kWh/m³)
- \( E_{H_2} \) = Hydrogen energy density (kWh/m³)
- \( f_{blend} \) = Hydrogen blend fraction
Electrolyser Size
\[ P_{electrolyser} = \frac{m_{H_2} \times 39.44}{CF \times \eta_{electrolyser} \times H_{daily} \times 1000} \]
Where:
- \( CF \) = Capacity factor
- \( \eta_{electrolyser} \) = Electrolyser efficiency
📖 Variables Legend
Symbol | Description | Unit |
---|---|---|
\( D \) | Steam rate | ton/h |
\( P_{steam} \) | Steam pressure | barg |
\( \eta_{burner} \) | Burner efficiency | % |
\( f_{blend} \) | Hydrogen blend ratio | % vol |
\( h_{steam} \) | Steam specific enthalpy | kJ/kg |
\( CF \) | Electrolyser capacity factor | % |
\( \eta_{electrolyser} \) | Electrolyser efficiency | % |
\( Q_{steam} \) | Annual steam required | ton/year |
\( Q_{heat} \) | Heat required | MWh |
\( m_{H_2} \) | Hydrogen demand | kg/day |
\( P_{electrolyser} \) | Electrolyser size | MW |
Hydrogen Stem Boilers: The Future of Industrial Heating
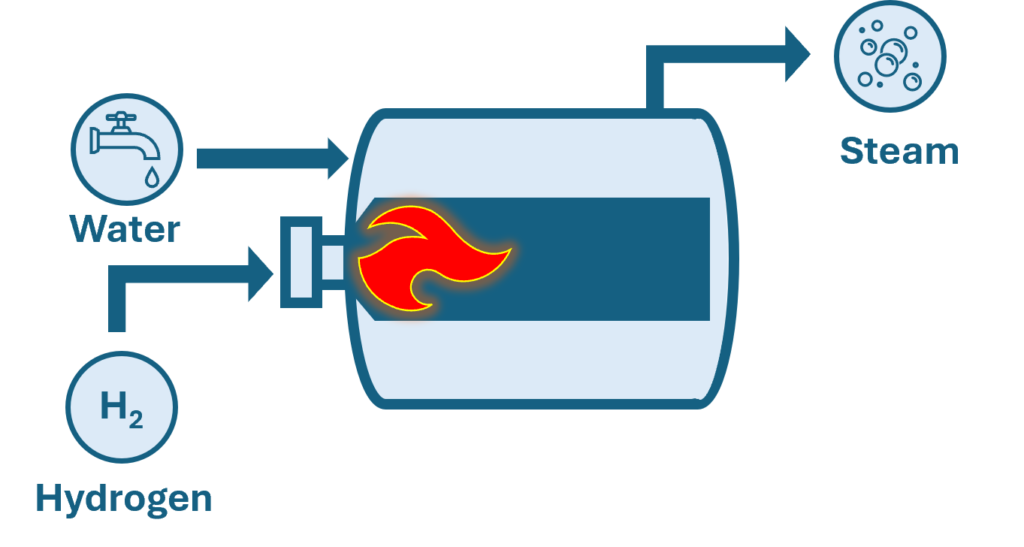
⚙️ How Hydrogen Boilers Work
Modern hydrogen-ready boilers use one of three approaches:
- • 100% Hydrogen Combustion: Specialized burners using H₂'s high flammability (4-75% in air)
- • Blended Fuels: Mix hydrogen with natural gas (20-30% H₂ in existing infrastructure)
- • Dual-Fuel Systems: Alternate between hydrogen and other fuels based on availability
💡 Key Advantage: Hydrogen boilers can achieve 95%+ efficiency when properly designed, compared to 85-92% for natural gas systems.
🌱 Why This Calculator Matters
Transition planning requires understanding:
- • Hydrogen demand vs storage capabilities
- • Infrastructure modification costs
- • Realistic emission reductions
- • Operational impact on steam output
Our tool helps answer:
"If I replace 30% of natural gas with green hydrogen, how does it affect my annual fuel costs and carbon footprint?"
⚠️ Critical Implementation Factors
Material Compatibility
Hydrogen causes embrittlement in standard steel pipes above 20% blends
Flame Speed Management
H₂ burns 7x faster than methane - requires modified burner geometry
NOx Tradeoffs
While CO₂ drops, hydrogen combustion can increase NOx by 50-200% without proper controls
📈 State of the Art (2024)
Technology | Max H₂ Blend | TRL | Key Players |
---|---|---|---|
Retrofit Burners | 25% | 8-9 | Honeywell, Siemens |
Dedicated H₂ Boilers | 100% | 6-7 | Mitsubishi, GE Vernova |
❌ Common Calculation Mistakes
- Ignoring hydrogen's lower volumetric energy density (3.54 kWh/m³ vs NG's 11.15 kWh/m³)
- Assuming linear efficiency gains with H₂ blending
- Overlooking compressor energy for H₂ storage
- Using LHV instead of HHV for electrolyser sizing
📋 Should You Switch? Decision Checklist
- ✅ Current natural gas price > $8/MMBtu
- ✅ Carbon tax > $50/ton CO₂
- ✅ On-site renewable energy available
- ❌ Existing boiler > 15 years old
- ❌ Steam demand varies > ±30% daily
Pro Tip: Start with 10-15% blending to test system compatibility before major retrofits.
© 2025 HowICalculate.com